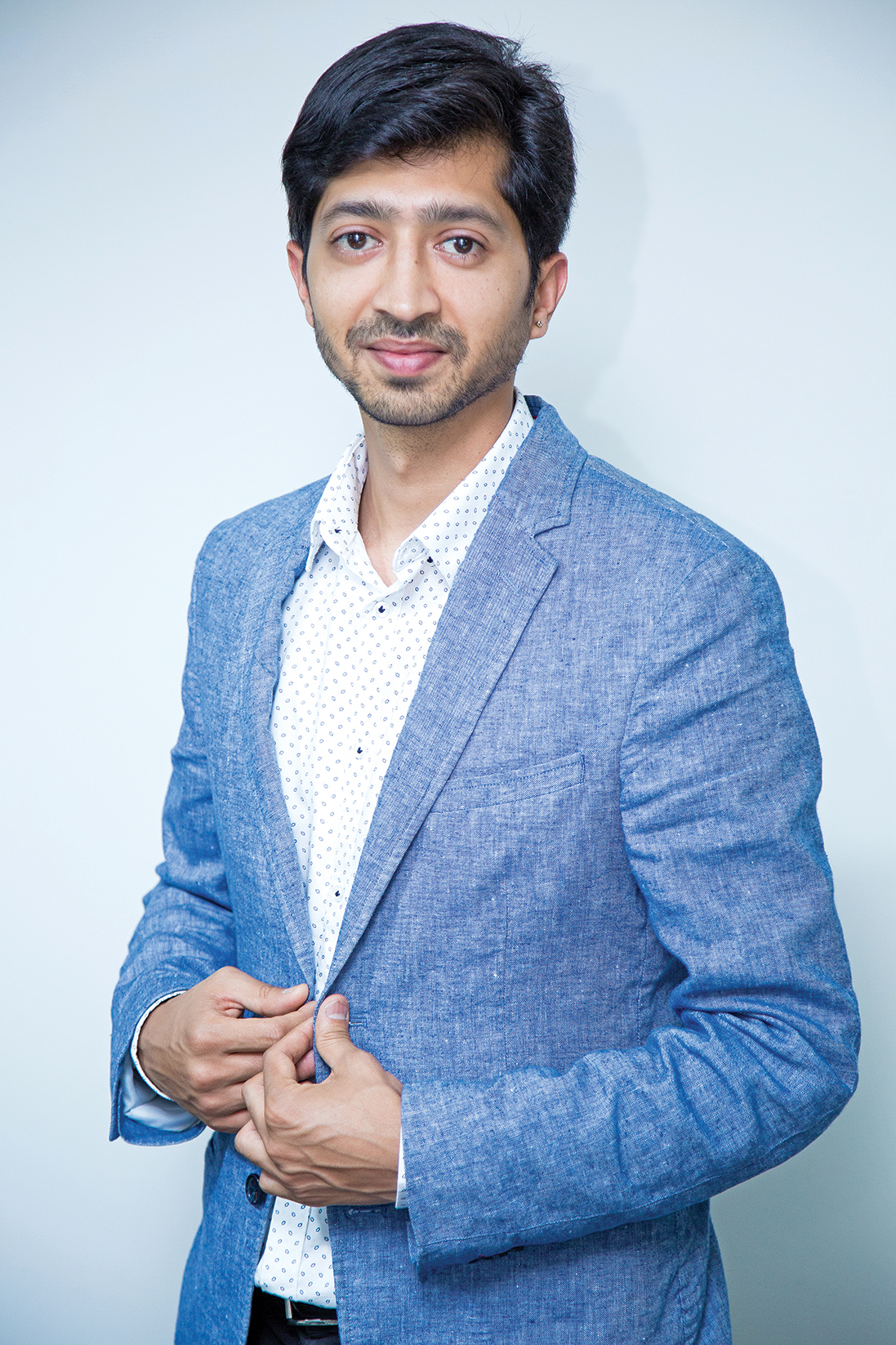
Director, Ghorahi Cemen
Can you briefly tell me about yourself and your company?
I have been in this business for eight years. I did my secondary studies in India and higher studies in England. After that I moved back to Nepal to work with my family and help them develop the cement business as well as Triveni Group, the parent company of Ghorahi Cement. Ghorahi Cement was formed in 2009 and came out as the largest clinker and cement manufacturing company in Nepal. Currently we are manufacturing 2,200 metric ton clinker as well as cement per day. As of now, we use the latest technology in cement industry available across the world. The equipments used to make the clinkers and cements are of Germany based company. We also produce OPC and PPC cement under the brand name ‘Sagarmatha’. We are soon introducing slag cement which will be cheaper to produce as well as cheaper for the general public.
What are the key qualities in cement that a customer should know before purchase?
When a person goes to the market to buy cement, their first question is, ‘sasto cement kun ho?’ (Which is the cheapest cement), and that is where people go wrong. In fact, their first question should be ‘what is the quality of the cement?”
I also recommend people to take a basic study on the types of cement and other construction materials appropriate for the type of building and land. People also say that cement should be dark in colour and not of light colour, which is a completely wrong notion. I don’t think the colour of cement has anything to do with the strength of the cement.
The service should also be the key focus because a construction company’s job is not just to provide construction materials but also to provide engineering and construction parameter assistance, which we here at Sagarmatha Cement have been providing to our customers especially after the April earthquake.
What are the major challenges that cement industries are currently facing? What type of assistance can the government provide?
We are a power deprived industry; without electricity none of the industries in Nepal can run to full capacity. The second issue is the lack of expert manpower. Although Nepal is exporting manpower to foreign countries, the cement industry is a very technical industry. Just having a machine is not good, we need the expertise. So, we are currently lacking those people who can teach the new generation, and to do so we have to get people from abroad, get them to stay here for months or years which is costly. The third challenge is transportation. Just being able to produce huge capacity is not enough. If there is no transportation services to transfer the produced goods to the market and people who need it, mainly in rural areas, hills and mountain regions, business suffers. Transportation has been a big problem whether to deliver the finished products or import raw materials. However, the government of Nepal has been very supportive when it comes to protecting local and domestic industries. They have applied enough custom duty for import of cement so international cements can’t come for cheap. But, right now what we need is infrastructure development where our roadways are better so vehicles can carry more capacity on the roads. Even if we try to provide cement at cheap and affordable pricing, the added transportation costs substantially increase the price. Sometimes, 20% cost of the cement is the transportation cost which creates artificial scarcity and the ones greatly affected by this is the general public. So, this is the problem that the government needs to tackle.
Cement Industry in Nepal has crossed almost half a century. In these 50 years, cement manufacturing technologies have also evolved. What types of technologies are currently being used and what is the future?
I am very proud to say that our Chairman of Triveni Group, Purushotam Lal Sanghai, was the first from the private sector to get a licence for cement manufacturing in Nepal. So, we have technically been the first private cement manufacturers in Nepal. Before that it was only Hetauda and Udaypur cement, both owned by the government. When we started manufacturing cement, we imported clinker from India. We used to only grind and package the cement. When clinker manufacturing started setting up in Nepal almost eight years ago, technology became a big question. For cement grinding, sophisticated technology wasn’t needed. It was similar to grinding spices, but in huge bulk. But when it comes to making clinker, it has to do with heat balance and making sure that the temperature is right. So, expert technology is needed to manage such temperatures. When we started our industry, we bought German technology equipment, although the cost of buying such equipment was 35-40% higher, but it is regarded as the best technology in the world. We did so because even though the capital cost is higher, the production cost will be much cheaper, and we are happy that we made that decision.
All large industries are investing in ensuring that they are environmentally friendly. If the government finds out that a company is not following the environmental parameters, it will be shut down. So when the companies are making investment of such amounts, they don’t cut corners, they make the best investment. Also, because the market in India is getting saturated, experts are now moving to Nepal and working with the best industry. Even international suppliers have set up offices in Nepal. They are all here because they see Nepal as a potential country. In clinker manufacturing, Nepal is considered a top country using the best technologies. I don’t think any industry in Nepal is compromising on technologies. New technology will help the industry reduce power and fuel consumption, and the cost of operation, so why would industries not be interested to invest in the technology?
Industries, especially construction industries, are said to be a source of environment harm and waste. How is the industry tackling such issues?
For Ghorahi Cement, 44% of the factory’s land is covered with trees. Almost 70 different varieties of trees have been planted and we have almost 35,000 trees on the factory land. So if you measure the oxygen that 35,000 trees are giving out versus the carbon that the factory is producing, it just completely changes the emission factor. The companies and industries are also engaged in various CSR programs and the government is taking a serious interest in CSR programs. Companies have to put 1% of their net profit into CSR. In the case of Ghorahi Cement, we have tied up with schools and colleges around Ghorahi, Dang. We have opened two-month internship and students can apply for that. We provide free electricity to the schools in Ghorahi area, help them during events, and a lot of other facilities so that education can be uplifted. Also in the villages, we have done sanitary and agricultural programs to uplift living standards.
In early January this year, construction contractors blamed cement and steel manufacturers for creating ‘artificial price hike’ of cement and steel in Nepal. Your comments.
Yes, there was a price hike. I think the price hike was a bit more than what should have been. I feel consumers deserve affordable materials for construction. If the construction materials are expensive, the economy will never grow. But, there were certain reasons for such price hike. One of the main reasons was the Raxual border. Raxual border kept some embankment on unloading of railway racks. The railway racks that carried 3,000 tons of raw materials like coal and clinker, they have all been disallowed to unload on the Nepal side because of environmental concerns raised by people around the area. The local people protested and stopped them from unloading which created scarcity of raw materials. As coal wasn’t available which is the most important raw material to make clinker, and imported clinker also being unavailable to make cement, it created ‘artificial scarcity’ of raw materials in the market. And as usual, when there is scarcity, prices go up. Many industries took extra advantage of the event and increased it to more than they should have.