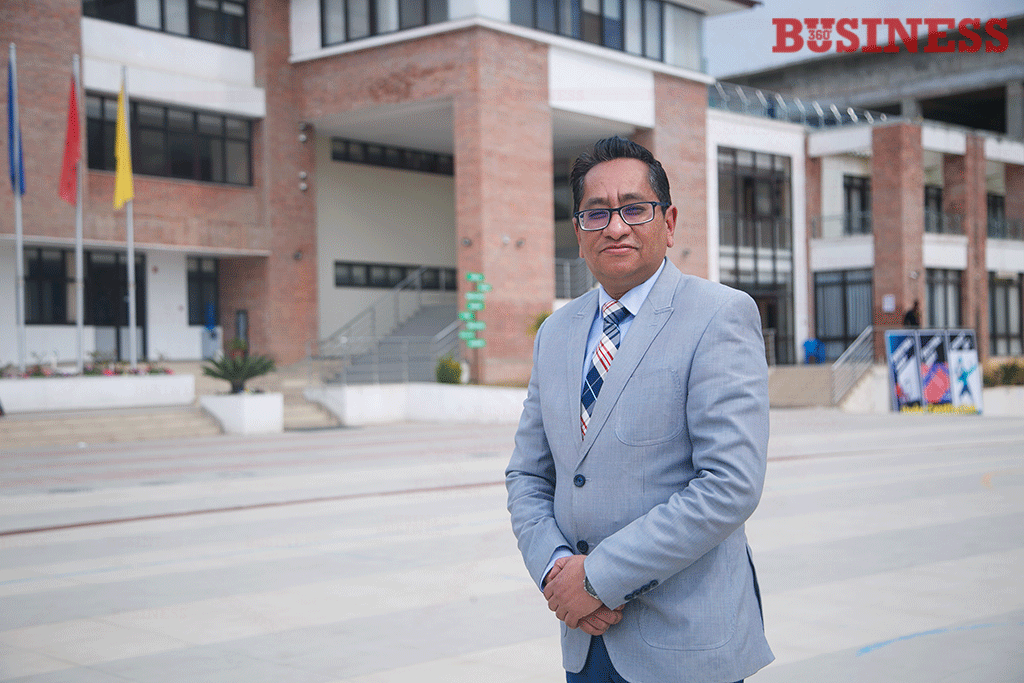
Krishna Ram Jaki Banjar is the Managing Director of Guru Ganesh Light Block Udhyog. The company manufacturers new-age green building material called Autoclaved Aerated Concrete (AAC) blocks which are light in weight and high in strength. The company was established in September 2016 and began operations in 2018. Currently, the company offers three AAC block variants of 4, 6 and 8 inches in breadth, all in 24-inch length and 8-inch height, and priced at Rs. 175, Rs. 260 and Rs. 335 respectively.
What is ACC block?
AAC block was invented in mid-1923 in Sweden. It is also known as Autoclaved Cellular Concrete (AAC) or Autoclaved Lightweight Concrete (ALC). The trend of AAC blocks started almost two years back in Nepal. AAC blocks are a substitute for red bricks and the production process is fairly simple.
AAC products are made using slurry mix containing fly ash, cement, lime and aerating agent. The slurry is poured and moulded to form light-weight blocks. The high-pressure steam-curing mechanism in the autoclave facilitates the curing process of the moulded lightweight concrete, producing physically and chemically stable products that weigh about 1/5 of normal concrete. AAC products contain millions of tiny non-connecting air pockets yielding superior thermal insulation property.
For a project developer, it means effective cost construction. For those who are environmental conscious, it means eco-friendly products, and for those who occupy buildings built with AAC blocks, it means better safety and lower energy costs for cooling and heating. Basically, it all translates to a better world for future generations.
What are the benefits of AAC blocks compared to red bricks?
Being lightweight is one of the biggest benefits of AAC blocks. AAC blocks are bigger in size and almost three times lighter than red bricks, meaning less load. It also means that AAC blocks are cost saving in terms of labour, cement and other construction materials used.

These blocks have microscopic pores resulting in less thermal conduction which maintains the inner temperature to be warm during winters and cool during summers which eventually results in lower usage of electricity. AAC blocks reduce up to 25-30% cost saving in AC/heater. The pores also enhance sound absorption feature of AAC blocks; therefore, these blocks are best for construction of big buildings. AAC blocks are fire resistant and highly suitable for modern housings or buildings. They offer fire resistance from 2-6 hours depending upon the breadth of the block. AAC blocks also have high resistance to water penetration than red or clay bricks.
Along with being lightweight, the structures built using these blocks are stronger, reliable, safer and have high earthquake resistance than those built using red bricks as the earthquake impact is directly proportional to the weight of the structure.
What are the important measures to be considered while using AAC blocks?
- There are a few simple yet important measures:
- During stacking of AAC blocks, they should be kept on dry and plain area to evade damage or contact with moisture.
- The blocks are to be cut using tools like hacksaw or rotary cutter.
- The blocks should be dipped in water and taken out immediately. Only the area in which mortar is to be applied should be dipped.
- The mortar mix should be of 1:6 ratios of cement and sand, mortar thickness should be kept limited to 10-12 millimetres and water curing is to be done only for the mortar joints.
- After every 1.2 metres, reinforcement coping beams should be kept.
- Minimum plastering is required on AAC block walls. It is important to have electric and sanitary chases done before wall plaster.