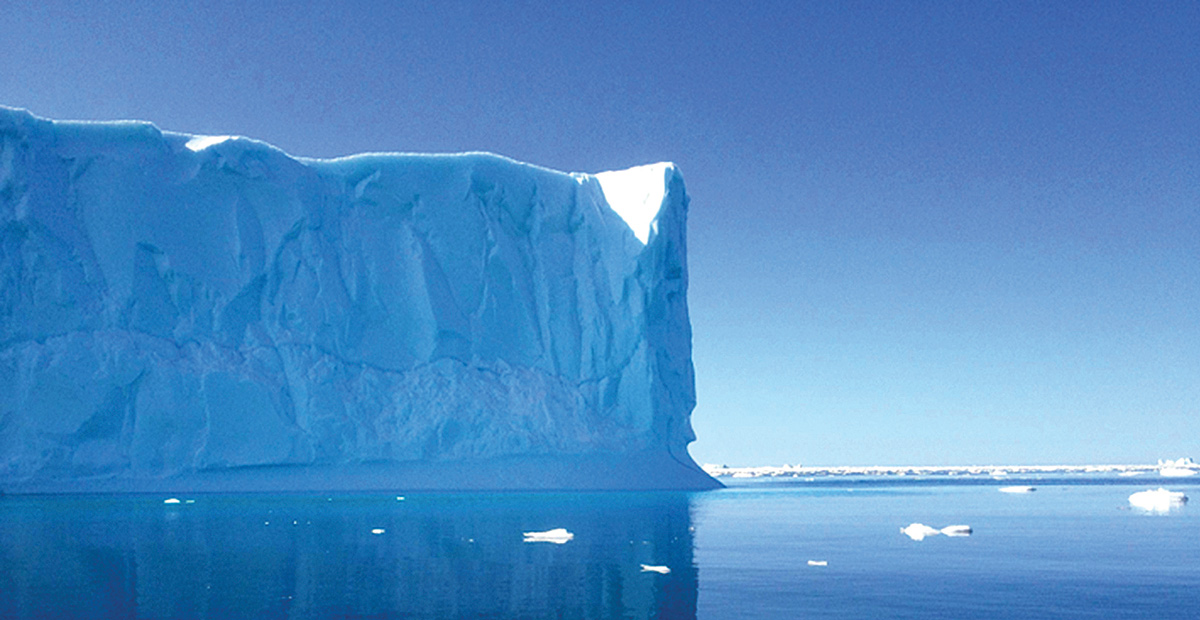
As human beings and organisations, our goals are always to increase production, our product reach and create awareness of our brand. Most of our energy is channelised into creating an increase.
But what about maximum utilisation of what we have, ensuring optimisation and obtaining the best value out of what we already have. The whole idea of tapping the non-identified cost and production loss was the genesis of the concept and term Hidden Factory, way back in 1977.
What quality guru Armand Feigenbaum coined five decades ago still holds strong. About 15% to 40% of company’s total effort is untapped or lost during production which is un-accounted or not factored in production or product costing.
That unrecognised, unaccounted, hidden cost and production loss is called The Hidden Factory. Agree or not the size of this hidden factory even after five decades continues to grow unless tapped.
The set of activities, controls and sub processes performed result in reduction of quality and efficiency of any business. The operational processes will result in increase of overheads on the product cost. These increased overheads are mostly not accounted for in product costing by most companies and the impact of this unidentified cost can be directly seen on the bottom line.
Assess the size of your Hidden Factory
Traditionally, costing of a product is done as raw material + direct labour + admin cost + other cost. However, no where do we budget for repairs, reworks, delays in production, unplanned production downtime, etc. All these inefficiencies cost us time, time translating into money, product and tools. This runs wide and deep in any organisation costing billions of rupees to companies that choose to overlook the same. If you need to reduce the parallel universe running within organisation we need to first estimate its size and what’s contributing to it. The fastest and easiest way to start is by measuring and optimising Overall Equipment Effectiveness (OEE). This is a complete measure to assess the production availability, overall performance and quality. OEE can be measured for each product line, organisation as a whole, overall service inventory, etc.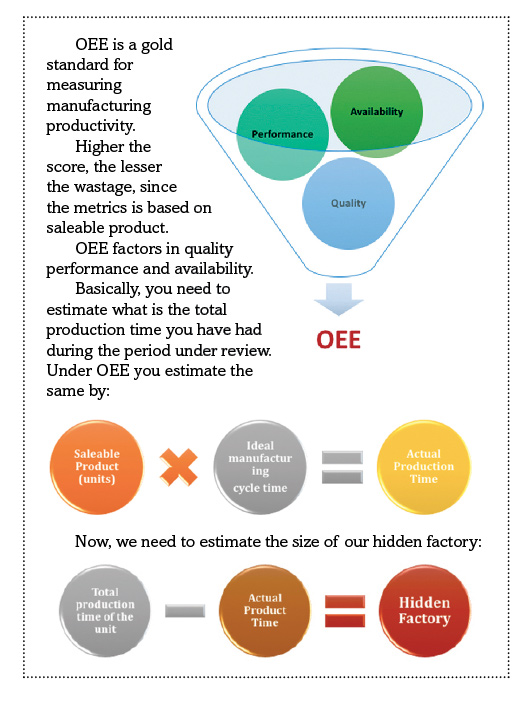
What constitutes the Hidden Factory?
Now that we know the size, we need to ascertain what is contributing to it. This hidden factory is not caused by one activity or process, it’s a contribution of many activities and sub-processes. A few examples commonly seen across industries:- Planned downtime not budgeted in production costing
- Incorrect timing of planned downtime,
- Non-budgeting of idle labour cost during downtime either planned or unplanned
- Unplanned break downs
- In production wastage
- Non estimation of standard direct labour hours for different production lines
- Loss in performance due to incorrect machine alignment, incorrect calibration, temperature settings, etc.
- Inadequate preventive maintenance
- Loss in product quality, resulting after works/ warranty claims
- Production bottlenecks not considered for overall capacity assessment
- Overtime due to bottlenecks
- Non assessment of root cause of repeated scrap in each shift or production run. Small scrap per shift does not matter but cumulatively number over each shift run high.
- Excessive repairs and maintenance due to mis-usage of equipment and machinery.
- Rush of doing activities, resulting in re-doing of the activity or afterwork. Both material and money.
- Inadequate training of new joinee resulting in wastage, scrap, rework, etc.
- Labour inefficiencies resulting in operational inefficiencies
- Cost of missing C-value spares, single spare does not cost but over a period of time its cumulative value is high.
- Delay in reporting quality reports, will impact the next production line, before the issue is fixed.
Automation: The key to the future
As per a Harvard Business Study on Hidden Costs between manufacturing companies in the USA and Japan, the variance of the impact for both direct production overheads and the hidden factory varied by 10% to 20% directly on account of level of automation. Japan managed to reduce its overall production overhead by 9% in comparison to USA only due to the advanced automation of the plant and non-direct functions like finance, labour management, maintenance, etc. Anyone from the manufacturing industry will agree 10% of a direct difference can do wonders to the bottom line. As per research and various global studies, automation is the easiest and most effective way to address the overheads associated with the hidden factory. This can also be seen in the above comparison of industries in USA and Japan.Ever growing Nepal
As per the latest World Bank Report, the beautiful land locked Himalayan country, is the only country even in between the pandemic to have a double-digit growth at an exponential speed. In 2016, manufacturing and service contributed to 66% of the overall GDP of the country. In spite of having varied heavy manufacturing industries and related services, the levels of automation on all fronts of production, data tracking, data analysis, etc. have been extremely low. Rather to say, it’s almost pathetic. This lack thereof, has resulted in increase and direct impact on cost of processing each transaction and cascading into product costing. The overall impact of this cost is borne by the manufacturers and people at large, making all essentials more expensive than any of our neighboring countries. Perhaps it’s time for us to wake up and break our blinders. The need of the hour is a more balanced approach in managing overheads cost more effectively by: Firstly, by analysing the hidden factory, secondly, assessing the sources and lastly, going down the path of automation and system stability. Hope you embark on this journey of automation and have a strong leash on your Hidden Factory.
Published Date: September 29, 2021, 12:00 am
Post Comment
E-Magazine
RELATED Ringside View